PLC, HMI, VFD-Inverter, Sensor and Motion Controller
Programmable Logic Controller (PLC)
Definition: A PLC is a ruggedized computer used for industrial automation to control machinery, processes, or systems. It can handle multiple inputs and outputs, both analog and digital, and is programmed using specialized languages such as Ladder Logic, Structured Text, or Function Block Diagram.
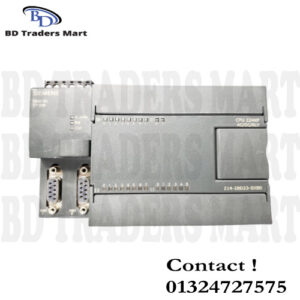
Key Features:
- Robustness: Designed to operate in harsh industrial environments.
- Real-Time Control: Provides precise timing and control for manufacturing processes.
- Programmability: Easily reprogrammable to accommodate changes in processes.
Applications:
- Assembly lines
- Robotics control
- Packaging machinery
Human-Machine Interface (HMI)
Definition: An HMI is a user interface that connects operators to the controller for an industrial system. It allows operators to monitor and control processes visually through graphical displays and input devices like touch screens, keyboards, or buttons.
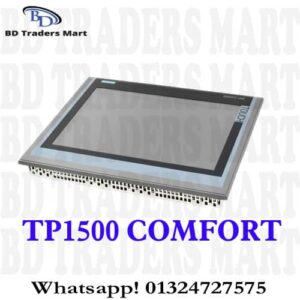
Key Features:
- User-Friendly: Intuitive interfaces with graphical displays.
- Real-Time Monitoring: Displays real-time data from the system.
- Control Capabilities: Allows operators to input commands and adjust parameters.
Applications:
- Supervisory control in manufacturing plants
- Monitoring energy usage in facilities
- Operating machinery remotely
Variable Frequency Drive (VFD) / Inverter
Definition: A VFD is an electronic device that controls the speed and torque of an electric motor by varying the frequency and voltage of its power supply. It’s also known as an inverter when it converts DC to AC.
Key Features:
- Energy Efficiency: Reduces energy consumption by adjusting motor speed.
- Process Control: Provides precise control over motor speed and torque.
- Soft Start: Gradually ramps up the motor speed to avoid mechanical stress.
Applications:
- HVAC systems
- Conveyor belts
- Pumps and fans
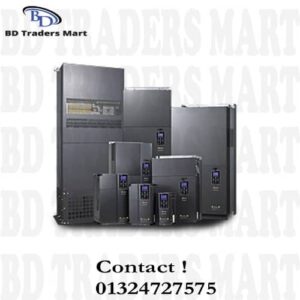
Sensor
Definition: A sensor is a device that detects and responds to changes in environmental conditions or physical properties such as temperature, pressure, proximity, and more. It converts the detected information into a signal that can be measured or read by a controller or operator.
Key Features:
- Accuracy: Provides precise measurements.
- Variety: Available in numerous types to measure different parameters.
- Reliability: Essential for consistent and accurate monitoring.
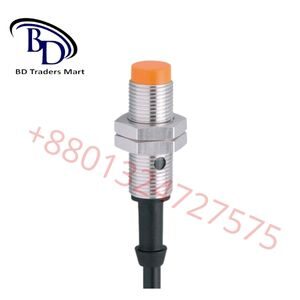
Applications:
- Temperature control in HVAC systems
- Proximity detection in robotics
- Pressure measurement in hydraulic systems
Motion Controller
Definition: A motion controller is a device that controls the movement of mechanical systems. It is used to achieve precise positioning, speed, and acceleration control of motors and actuators in automation systems.
Key Features:
- Precision: Ensures accurate positioning and movement.
- Synchronization: Coordinates multiple axes of motion.
- Flexibility: Supports various motion profiles and trajectories.
Applications:
- CNC machines
- Robotics
- Automated assembly lines
Integration Example
In a typical automated manufacturing system, these components work together to achieve efficient and precise operations. For instance:
- Sensors detect the position of a product on a conveyor belt.
- The PLC receives this data and sends commands to the VFD to adjust the conveyor speed.
- Operators use an HMI to monitor system performance and make adjustments.
- A motion controller ensures that robotic arms place components accurately.
- The VFD controls the speed of motors driving various parts of the system to optimize energy use and process efficiency.
Expert Inverter-VFD Repair Services: Ensuring Uninterrupted Operations
In today’s industrial landscape, variable frequency drives (VFDs) and inverters play a critical role in controlling motor speeds and enhancing energy efficiency. When these devices malfunction, it can lead to significant downtime and loss of productivity. That’s why professional inverter-VFD repair services are essential for maintaining smooth operations and avoiding costly disruptions.
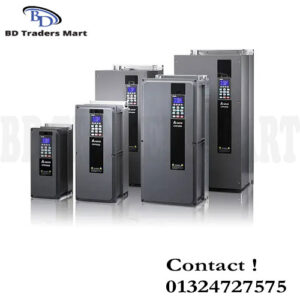
Understanding Inverters and VFDs
What Are Inverters and VFDs?
Inverters and VFDs are electronic devices used to control the speed and torque of electric motors. VFDs, in particular, are employed to vary the frequency and voltage supplied to the motor, which adjusts the motor’s speed to meet the demands of the process.
Common Issues with Inverters and VFDs
Despite their robust design, inverters and VFDs can experience a range of issues, including:
- Overheating: Often caused by inadequate ventilation or excessive load.
- Electrical Noise: Can interfere with the device’s operation and lead to erratic performance.
- Component Wear: Over time, components such as capacitors and transistors can degrade, leading to failures.
- Software Glitches: Firmware or software issues can disrupt communication and control functions.
The Importance of Professional Repair Services
When your inverter or VFD fails, it’s tempting to attempt a quick fix or replace the unit entirely. However, professional repair services offer several advantages:
Expertise and Experience
Certified technicians have the knowledge and experience to diagnose and repair a wide range of issues. They use advanced diagnostic tools to pinpoint the root cause of the problem, ensuring a precise and effective repair.
Cost-Effectiveness
Repairing an existing unit is often more cost-effective than purchasing a new one. Professional repair services can restore your equipment to optimal condition at a fraction of the replacement cost.
Reduced Downtime
Expert repair services can significantly reduce downtime. Quick and efficient repairs mean your operations can resume with minimal disruption, saving you time and money.
Quality Assurance
Reputable repair services provide warranties on their work, giving you peace of mind that your equipment will perform reliably after the repair.
Choosing the Right Repair Service
When selecting an inverter-VFD repair service, consider the following factors:
Certification and Training
Ensure the technicians are certified and have received proper training from recognized institutions or manufacturers. This ensures they are up-to-date with the latest repair techniques and standards.
Diagnostic Capabilities
Choose a service that uses state-of-the-art diagnostic equipment. Advanced diagnostics can detect underlying issues that might not be apparent during a visual inspection.
Turnaround Time
Ask about the expected turnaround time for repairs. A service that offers quick and efficient repairs can help minimize downtime and get your operations back on track faster.
Customer Reviews
Look for customer reviews and testimonials. Positive feedback from other businesses can indicate the reliability and quality of the service.
Preventive Maintenance Tips
In addition to professional repair services, regular preventive maintenance can help extend the life of your inverters and VFDs. Here are some tips:
- Regular Cleaning: Keep the unit free from dust and debris to prevent overheating.
- Routine Inspections: Regularly inspect components for signs of wear or damage.
- Firmware Updates: Keep the firmware updated to ensure optimal performance and security.
- Proper Ventilation: Ensure adequate ventilation to prevent overheating and extend the lifespan of the components.
For expert inverter-VFD repair services, contact us today. Our certified technicians are ready to provide the high-quality repair and maintenance services you need to keep your business moving forward.